Your desktop power supply has been running for many years, still maintaining good performance, which is indeed a remarkable feat! However, the output power connector selection has some shortcomings, with the 3-pin header type connector not being suitable for this power output, which can easily lead to cooling issues.
It’s time to upgrade your power supply now! Consider using a better output power connector, such as MOLEX or SATA interfaces, which are more reliable and universal. Additionally, improving the heat dissipation design, such as adding heat sinks or improving the heat dissipation ventilation system, will also help to ensure stable operation of the power supply.
Furthermore, using more modern power management technologies, such as DC-DC converters or switching power modules, can improve the efficiency and reliability of the power supply. In summary, it’s time to upgrade your power supply to make it more stable, reliable, and efficient!
Old regulator schematic
A true desktop power supply typically comes with features such as adjustable current limiting and a display for voltage and current. However, I chose to keep things simple and didn’t add these features to avoid spending too much time. Fortunately, these features can be easily added later, located between the power supply output and the load.
The LT1083 voltage regulator IC has been discontinued and can only be purchased from China, but these products are likely to be counterfeit. I found that the MIC29752 is very similar, and it has some additional features, such as an enable pin, which makes it easier to control the power supply. This is very beneficial for me, as I want to remove the original power switch and use some kind of solid-state design. If there wasn’t an enable pin, I would have to add some MOSFETs.
The new power supply
I often need an auxiliary power supply voltage, so I used an LM317 voltage regulator to add an adjustable auxiliary output. With a small trimmer potentiometer, the output voltage can be easily adjusted. However, in the first PCB revision, I made a serious mistake, the welding pad wiring was completely wrong (based on L78M design). As a result, when the circuit board was powered on, it short-circuited quickly, leaving a small hole. This failed lesson taught me that details and accuracy are extremely important when designing and soldering circuit boards.
I also noticed that the LM317 in SOT-223 packaging has a higher thermal resistance and higher current limit compared to the SOT-252/DPAK packaging, which seemed unusual to me. Therefore, I purchased both types and experimented with them on the circuit board. As a result, I found that the SOT-223 packaging can dissipate more power before self-thermal limiting. I had expected the opposite to be true, but the result was contrary to my expectations. Fortunately, the SOT-223 packaging can fit well into the SOT-252 packaging, solving my problem.
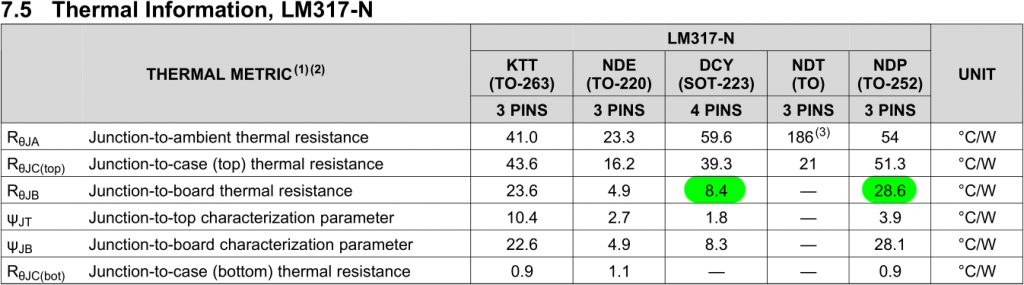
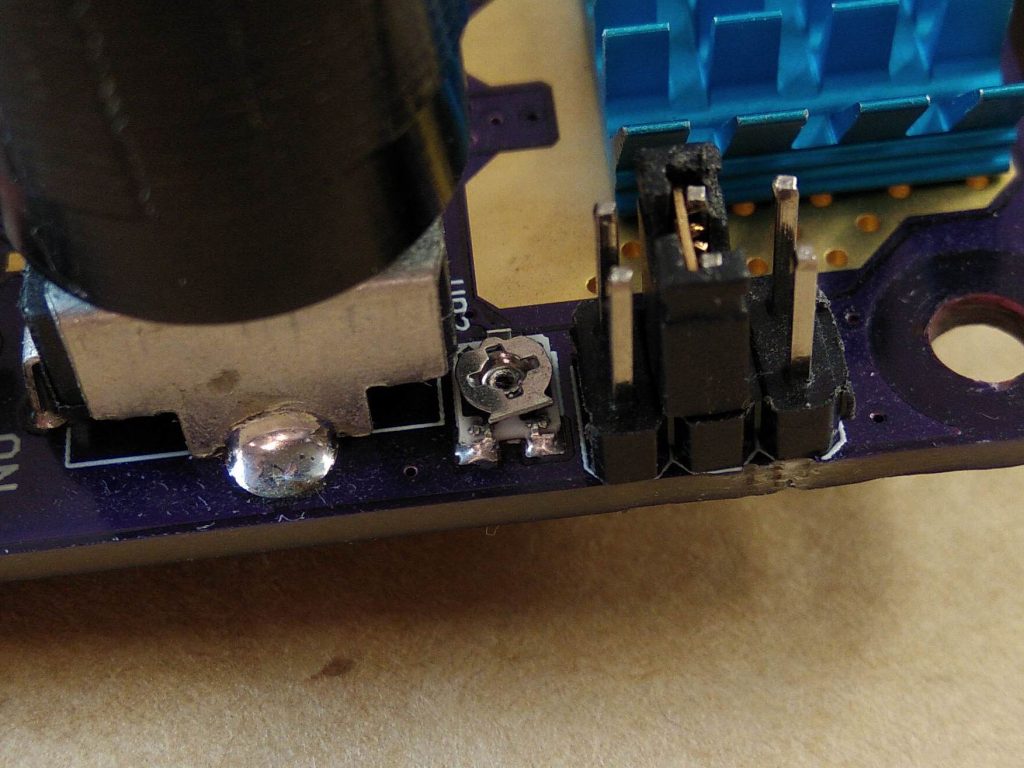
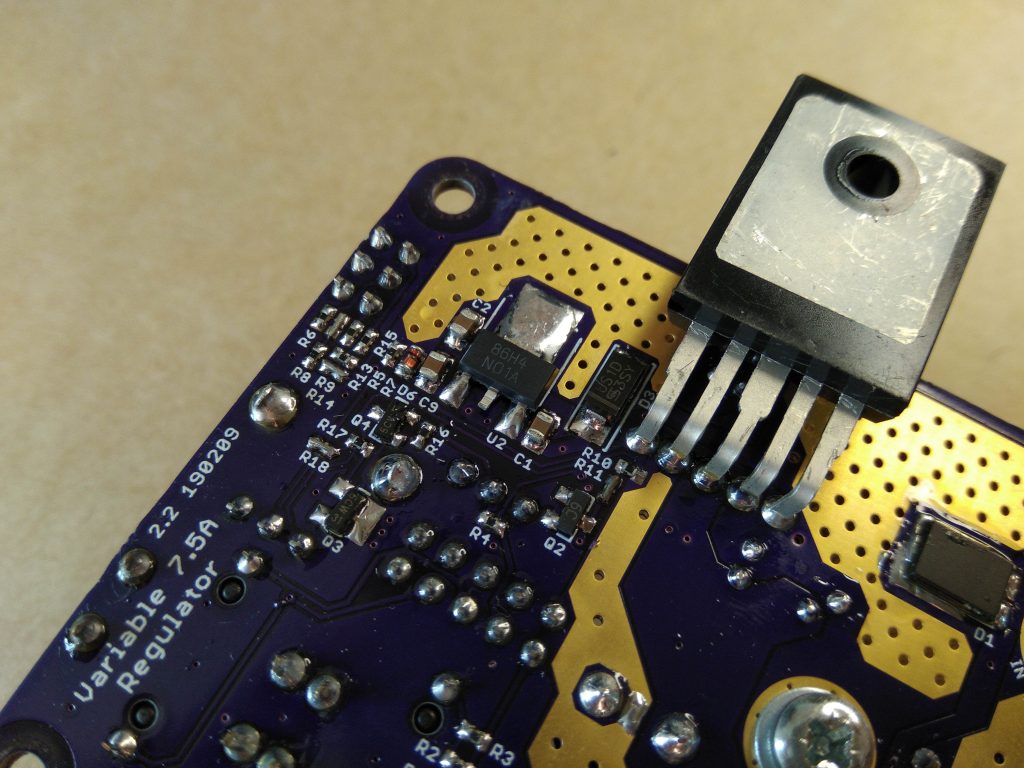
The old power supply also had a 6-way voltage range selector jumper: 3V, 5V, 7V, 9V, 12V, and 19V. However, I found that I only needed to use the 5V, 12V, and 19V ranges, so I simplified the selector jumper to these three ranges in the new design. This not only makes fine-tuning the output voltage more convenient but also provides some fault protection to prevent accidental damage to the circuit when connected to a 5V circuit, where the voltage control knob might be turned all the way up to 19V.
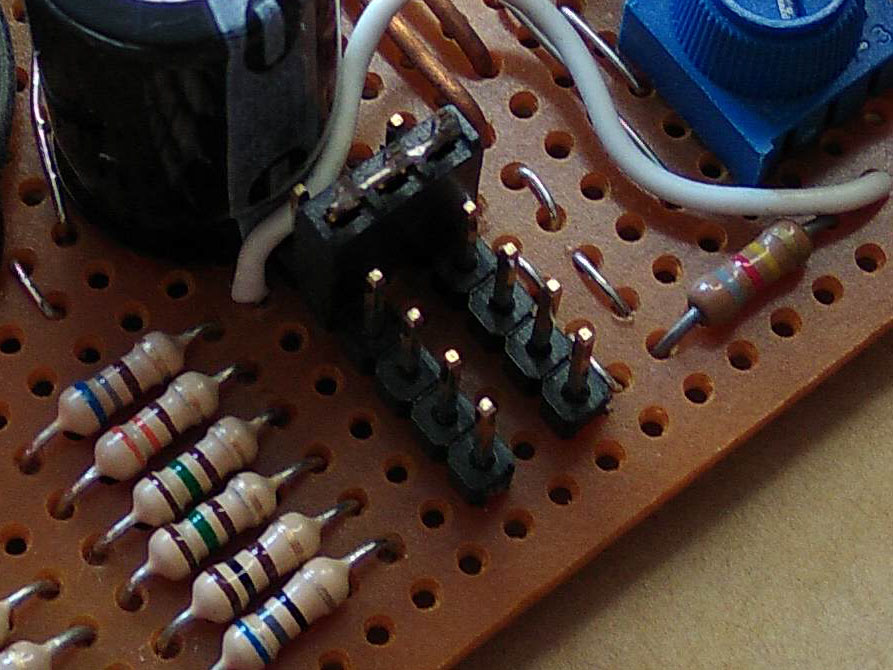
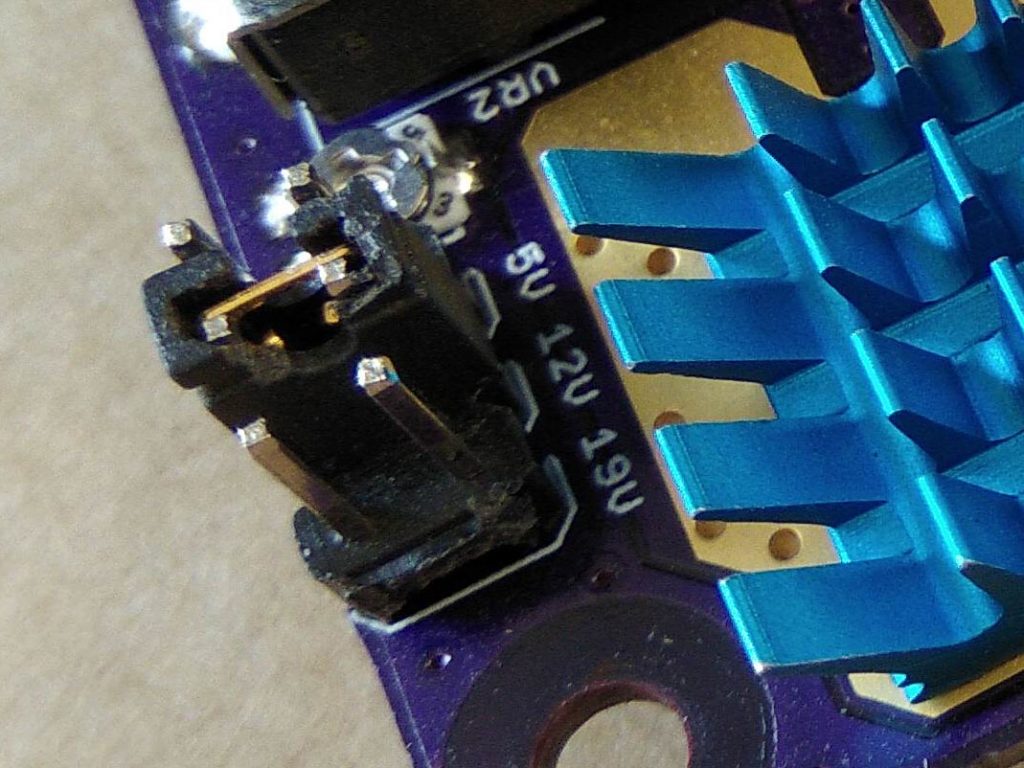
All these voltage regulator ICs require a minimum load current, typically 5-10mA, to maintain output voltage stability. Therefore, I added an 8.5mA current source to each output to ensure stable output voltage. However, the old power supply didn’t have any minimum load current configuration, but I never encountered any issues. This might be because the feedback resistor absorbed enough current to maintain output voltage stability.
Now, the power supply is controlled by 2 buttons with integrated LEDs, which are connected to a small, plug-in, fully analog control board for debouncing and controlling the enable pin of the main regulator IC. This control board can be replaced, allowing modification of the button and LED behavior, or even external control of the power supply.
Currently, the left button is used to turn off the power supply, and the right button is used to turn it on. When holding down the “off” button, the “on” button becomes a momentary button, which is very useful for short-term power-on testing.
The control circuit has more components than a typical latch comparator circuit because I want it to remember the on/off state for about 250 milliseconds after power-off, which is achieved through C2. This is because the laptop PSU tends to cycle on-off-on-off during overload periods, and I don’t want the regulator to reset to the off state in such cases. To achieve this, I also need to handle debouncing for simultaneous button presses when creating the momentary “on” button.
In the circuit, Q2 inverts the comparator output, and Q1 is required, otherwise Q2 would never turn off, as the current can flow through R8 and R4 to ground. I simulated the circuit using Falstad Circuit Sim.
Regarding the new output power connector, I really like securing the alligator clips to screws, and I also added screw terminals and some ordinary pins for low-current use. The input power connector is similar, including screws, terminals, and a 2.5mm DC jack for laptop power supplies. I forgot about banana plugs; otherwise, I might have thought of adding them too. There’s also a fourth screw near the board center, which can be used to bypass the input diode if needed.
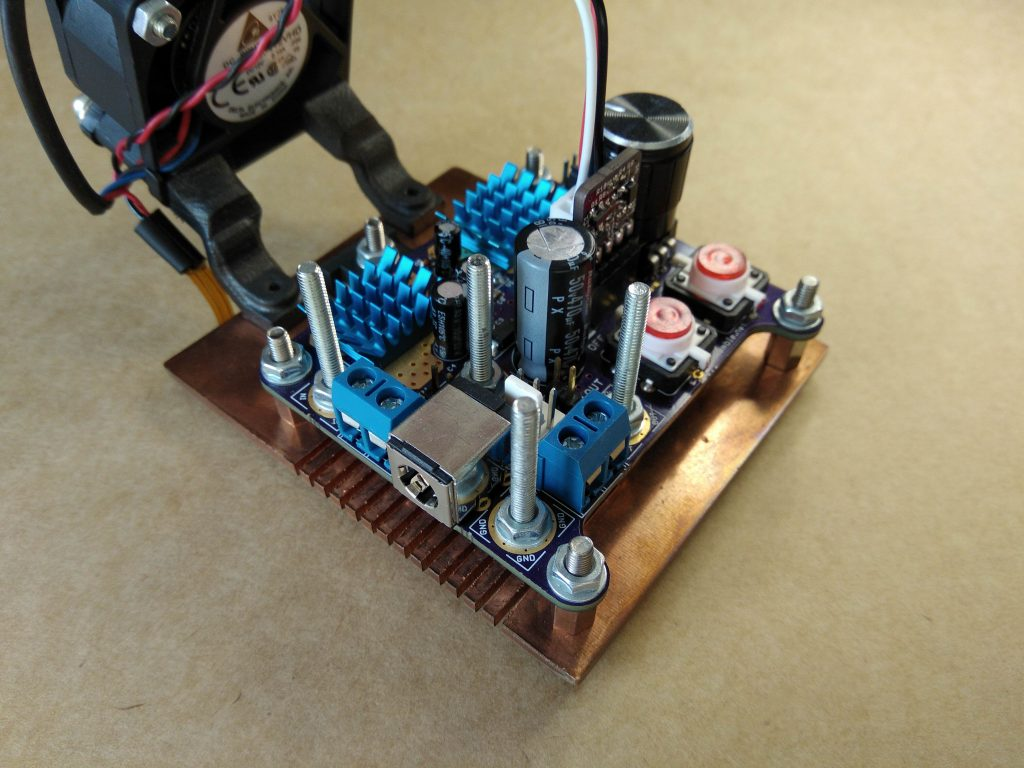
I also designed a new custom heat sink, which is intended to serve multiple purposes: it can be a solid mounting point for the PCB, add weight to prevent the power supply from being easily moved, and help keep the regulator cool. I used a 70x78mm 3mm thick copper plate, drilling several screw holes for the PCB and regulator, and cutting out some slots to aid in cooling and make it look more interesting!
After some testing, I found that the new heat sink didn’t perform much better than the old one. Due to its high thermal conductivity and heat capacity, it takes longer to heat up, but its design is not excellent for passive cooling.
I used a 3.3R 10W power resistor as a load, setting the output voltage to 5V to test the heat sink’s performance. The MIC29752’s thermal limiter kicks in at 125°C, reducing the output voltage to decrease current and heat, preventing further temperature rise. After a few minutes, the output voltage dropped to around 2.2V (with a current of 0.66A through the resistor), which means the regulator can only dissipate 11.2W while keeping the junction temperature at 125°C.
Calculating the heat sink’s thermal resistance, I got 7.13°C/W, which is a slight improvement over the original heat sink’s rated thermal resistance of 7.2°C/W 😛
The output was still slowly decreasing, but the regulator was oscillating slightly at around 16KHz, causing the large output capacitor to produce a quiet hissing sound, so I decided to stop the test. The LT1083 had no oscillation issues and can withstand temperatures up to 150°C.
A small fan, actually a quite powerful Delta EFB0412VHD, powered by the auxiliary output, installed at the back, greatly improved the situation. I also made a small control board with an ATtiny10 to control the fan based on the heat sink temperature, with a button to select auto/on/off. Setting the output to 5.7V, with a current of 1.7A or around 10W through the resistor, the regulator can easily dissipate 23W. The thermal imager showed the plastic top of the case at 68°C (the thermal imager couldn’t work on the copper heat sink due to its high reflectivity). I estimate the regulator can dissipate around 35W with the fan. Assuming the case can maintain a temperature of 25°C, the regulator can dissipate a maximum power of 66W.
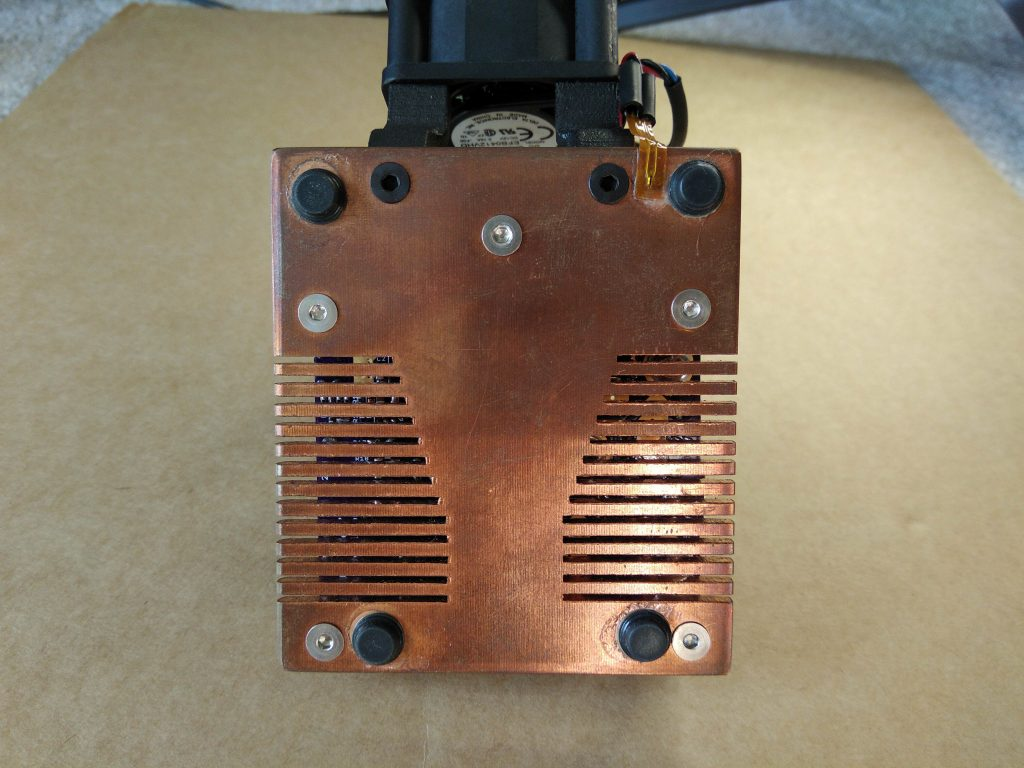
One downside of copper is that it easily tarnishes and loses its shine Also the rubber feet adhesive melts when the heatsink warms up.
Fan controller
Overall, this is a successful project! Now it has screws to secure the alligator clips, making it easier to use, and it’s heavy enough to prevent it from sliding around on the desk. Additionally, the cooling effect is better after installing the fan. I need to find time to make a current limiter and display board, but I think I’ll just buy a real desktop power supply instead, haha!
PCB designs, firmware and things can be found on my GitHub
Regulator schematic